Desalination plays a crucial role in securing sufficient freshwater supplies for a fast-growing global population and for a vast number of industrial purposed.
At the same time, regulators, the water industry and consumers are looking for ways to reduce cost and carbon emissions in desalination operations — primarily through improved energy efficiency or alternative energy sources. Engine Driven Pump
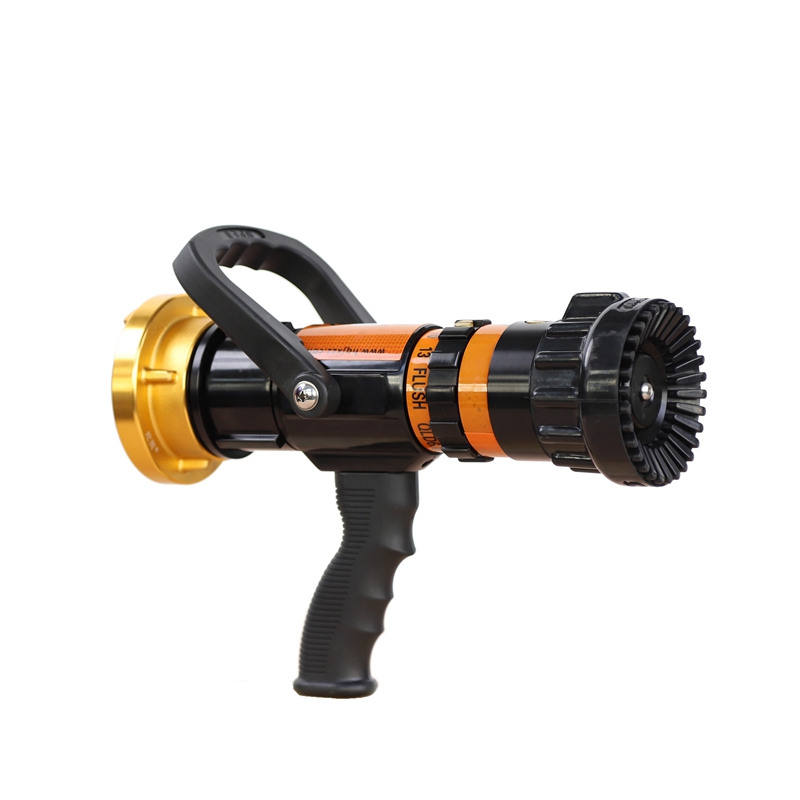
While reverse osmosis (RO) is recognized as the most effective way to generate fresh water from seawater, it is also an energy-intensive process. This leads plant owners and operators to optimize the energy efficiency of the plant and the power mix.
The choice of equipment and components defines the energy efficiency of a reverse osmosis (RO) installation, from initial design to later upgrades and retrofits. Often, increased efficiency can be achieved through small investments with a short pay-back time.
Moreover, sea water reverse osmosis (SWRO) plants require more flexibility to optimize the amount of flow that a plant must deliver, as demand and/or operating conditions fluctuate during the year
While centrifugal pumps are currently the dominant solution for large SWRO plants, axial piston pumps (a positive displacement technology) offer the best efficiency for high-pressure pumps.
In SWRO plants, the highest energy consumer by far is the high-pressure pump, which can reach up to 80% of the total specific energy consumption (SEC) of the SWRO plant. Hence, there is a need to ensure the highest efficiency high-pressure pump during all modes of operations to achieve the maximum reduction in SEC.
There is a fundamental difference in the underlying technology between centrifugal pumps (CF pumps) and axial piston pumps (AP pumps).
CF pumps generate flow and pressure “simultaneously.” The impeller inside the CF pump transfers kinetic energy (flowrate) to the water, and the system’s resistance to this flowrate translates some of the flowrate into pressure. Pressure and flow are linked, which is seen from standard CF pump flowcharts which is illustrated below in Figure 1.
A CF pump induces, through friction, kinetic energy into the water which in turn creates the pressure difference between inlet and outlet. This means that, without friction, no kinetic energy and no pressure increase.
This is why centrifugal pumps operate at relatively high rotation speeds for high flow/high pressure applications. A lot of kinetic energy needs to be induced into large volumes of water to have energy enough to lift the pressure at the CF pump outlet. This has the consequence that CF pumps cannot create flow or pressure lift without energy losses.
The various unavoidable loss mechanisms have the practical implication that the overall total efficiency of a CF pump is limited. Losses are unavoidable, as it is through the losses the work of the CF pump is done. Consequently, CF pumps’ typical max efficiency is around 91%, and this peak value is only achievable in very large pumps (flow rate > 3,000 m3/h).
AP pumps are fundamentally different to CF pumps. AP pumps belong to a family of pumps called positive displacement pumps. They are designed to mechanically seal between the high-pressure outlet and the low-pressure inlet. If the pump stops rotating, water cannot flow backwards through the pump.
Inside an AP pump, a plurality pistons moves/displaces water from the low pressures side to the high pressure (hence the name: displacement pump), and in doing so they will add whatever energy is needed to lift the pressure to the level required at the high-pressure outlet.
There are principally no fundamental loss mechanisms associated with this process that (at least theoretically) cannot be minimized to become negligible compared to the hydraulic work the pump does. The maximum efficiencies available in the market for typical RO pressures are around 91% - 92%. But there is no physical reason AP pumps for RO application in the future could not reach 95%, 96% or even 97% energy efficiency.
Figure 3 shows the efficiency of AP and CF pumps, assuming both are working at a constant outlet pressure of 60 bar in their best efficiency point. The efficiency difference in a 1,000 m3/d train is approximately 17% and 3% in a 25,000 m3/d train.
Even though the energy efficiency gap between AP and CF pumps decreases for larger flows, the absolute amount of kWh’s saved increases as the volume of water that flows through the pumps also increase. This is illustrated in Figure 4. The kWh’s saved at 3,000 m3/d is 850 kWh/day and 1550 kWh/d at 25,000 m3/d.
Pumps in SWRO plants do not run at constant flow and pressure conditions. Rather, they are exposed to variations which can occur over short and long timeframes.
These variations are driven by a variety of parameters, such as seasonal changes in sea water salinity; changes in production requirement, e.g. with high demand during warm and dry periods or during tourist peak months, and lower demand during other periods; and dynamic changes in electricity prices across seasons or even across 24 hours in a day.
AP pumps are a unique technology with almost constant energy efficiency profiles across both flow and pressure variations. This means that a SWRO system built with AP pumps has superior performance during the variations mentioned above, maximizing energy efficiency at any seasonal variations, to produce either the minimum specific power consumption or minimum specific cost consumption during the whole range of operational conditions.
In a real-life RO plant, several external parameters change dynamically.
Hence, it is often too simplistic to assess only one operational scenario to make the best decisions on plant design and choice of pump technology. As mentioned above, things that change include:
To illustrate the potential benefits of AP pumps, system calculations have been done for trains between 500 to 15,000 m3/d using efficiency data from Figure 3 and considered CF pumps run with variable frequency drives to better adjustment of the pressure and efficiency.
The two scenarios considered are summarized in Table 1:
Scenario 1: The system works at fixed flow, pressure and electricity price
Scenario 2: The system operates as in real life, where three different variables are taken place: different flows, pressure and electricity prices
The opportunity is here and now to accelerate toward carbon neutrality in desalination as in many other industries and communities.
So far, the desalination industry has primarily focused on optimizing the energy efficiency of the main equipment in order to cut down power consumption.
Solutions for greatly improving the power consumption through equipment with higher energy efficiency and more flexible operation are ready and proven. The upsides of investing in low carbon solutions are clear in terms of cost savings and making a substantial contribution to the climate-friendly operation of desalination plants.
An additional and potentially future key feature of an ultra-flexible AP pump-based SWRO plant is the ability to play an active role in balance grid power, particularly given that intermittent energy sources will play a larger role in the energy mix.
Smart and sustainable solutions in the desalination industry are readily available and offer opportunities to make cost and emission reductions go hand in hand.
Georg Herborg has held the role of director of innovation at Danfoss High Pressure Pumps since 2017. He oversees R&D activities, new product developments and the internal laboratory, where products and prototypes are tested and validated. He holds a Ph.D. in physics from the University of Aarhus in the field of atomic scale studies of metal oxide surfaces.

Emergency Pumps Francisco Jiménez-Castellanos is the global desalination manager at Danfoss High Pressure Pumps, responsible for the global business strategy in the desalination market. He has more than 11 years of experience within the pumps and seals business for desalination, water and power plants worldwide. Prior to his role at Danfoss, he held leading positions in Flowserve, heading the aftermarket commercial operations for France, Spain and Portugal.