In March 2014 my friend Steen Carlsen who is a power electronics engineer wrote a paper in which he wished to initiate the development of a portable and a stationary “Winding Tester” for electrical machines (motors, generators, and transformers). He had no knowledge of such a device being available, and thought it would be a tremendous benefit to shift from a “preemptive maintenance” protocol to a “replace when needed” protocol for electrical machines in any industry worldwide.
He still has no knowledge of such a device being available, and he believes that current winding testers — like the ALL-TEST Pro 7 — does not apply the same concept. 34 Awg Magnet Wire

When Steen told me about the paper recently — I believe we were discussing electric transportation — I didn’t even know there was such a thing as wear and tear of the insulation of copper windings in an electrical machine. It turns out there actually is, due to electromagnetic forces that act on the physical wires in such a way that they move/vibrate ever so slightly — causing the insulation of adjacent wires to rub against each other to the point where the insulation grind through or cracks resulting in short circuits. This, in turn results in heat and power loss, spiraling out of control until complete failure.
I wondered if the remedy against this — that Steen had now explained to me — might already be in use in the real world? This is something that is near impossible to research, because motors just work, until they don’t. A manufacturer of a product can state an expected lifespan of a product, e.g. a million miles for an electric motor in a car. But it will generally be guesswork, as the manufacturer cannot know the torque pattern, to which the motor will be exposed over time. Still, might they have this kind of monitoring of motor health implemented — perhaps undetected by experts like Sandy Munro? Not a chance, right?
With permission from Steen Carlsen I have enclosed his paper here and I would urge any tech savvy electrical machine nerds out there to help figure out if this concept is in actual use. My friend Steen and I are just curious, and our hope is that you — having maybe now heard about this concept for the first time ever — will be curious too, and maybe even implement it.
Here is a slightly edited excerpt of the paper as it was written almost 10 years ago:
Until this moment in history it has not been possible to monitor the development of wear in the insulation in electrical machines i.e. motors, generators and transformers. Not until deteriorated insulation has caused partial discharges, and thereby indicated an imminent fatal winding failure, has the wear hitherto been detectable. This paper presents a new means to monitor the development of the deterioration in the wire insulation in electrical machines and thus provide peace of mind for their owners.
The concept is based on monitoring the shift in the resonance frequencies of the resonance circuits constituted by the inherent inductance of the winding turn(s) and the (increasing) capacitance caused by the declining thickness of the layer of the lacquer insulation in the areas where the insulation gets worn.
The shift in resonance frequencies can be detected by measuring the machines winding impedances Z(s) as a function of the frequency.
Most electricians would diagnose an electrical machine by comparing the currents in its three phases or by using a comparative measurement of differences in the resistances of the three windings. But not until a fatal breakthrough in the wire insulation has occurred will one be able to detect any significant change in the resistances of the three windings nor any significant change in the phase currents. Thus, these methods cannot be used to predict the remaining lifetime until just before the machine is about to perish.
The following pages present a new concept for detecting wear in the winding insulation in electrical machines. This method also allows establishing which of the phase windings is about to perish.
Wear in electrical machines leads to reduced thickness of the lacquer insulation of the wires, which in turn, causes a change in the capacitance between adjacent (wire-) turns in the machine.
The detection of the changes in the capacitance can be done either in the frequency domain i.e. the impedance Z(s), and/or the time domain i.e. through the change in the propagation delay through of the windings.
Throughout the operational life of the machine and up to the moment of failure, the physical configuration, hence the number of turns and thus the inductance between any such areas will remain unaffected by the wear and tear of the machine. Hence, as long as the cores of the two adjacent turns in the winding have not yet shorted together, the inductance between the two areas remains unaffected by the wear. The capacitance, however, will increase by the wear of the insulation. Hence, as the insulation gets worn, the resonance frequency — associated with capacitance and the inductance between the two worn areas — will drop.
Note that already during the production of the machine, as the wire tension is applied by the winding machine, and the wire is drawn down to rest on top of the underlying layers, the deterioration of the wire insulation will be started.
You read that correctly. This is a non-invasive way of measuring the health of an electrical machine, while in operation! Had it not been for Steens Carlsen’s lifelong merit, I would have thought this was impossible.
The letter is a 17 page long document of considerable technical detail of how this way of measuring wear in electrical machines could be implemented. It is way over my capacity of understanding in detail, but I get the main points.
To summarize a few questions that come to mind:
Considering the acceleration in the electric vehicle disruption, I find this kind of thing exceedingly relevant. Think about it, most electrical machines have historically been chugging along in mostly static, confined, and stable environments, but now millions of EVs are getting out in the wild, in a comparable much harsher environment of vibration, extreme temperatures, and violently shifting power loads (acceleration, recuperation).
I would encourage you to comment below if you have any knowledge of this novel way of monitoring electrical machines. Maybe it’s not even news? Or even possible? But if it is, wouldn’t it be cool if someone used this to make electrical machines even more reliable?
Jesper had his perspective on the world expanded vastly after having attended primary school in rural Africa in the early 1980s. And while educated a computer programmer and laboratory technician, working with computers and lab-robots at the institute of forensic medicine in Aarhus, Denmark, he never forgets what life is like having nothing. Thus it became obvious for him that technological advancement is necessary for the prosperity of all humankind, sharing this one vessel we call planet earth. However, technology has to be smart, clean, sustainable, widely accessible, and democratic in order to change the world for the better. Writing about clean energy, electric transportation, energy poverty, and related issues, he gets the message through to anyone who wants to know better. Jesper is founder of Lifelike.dk and a long-term investor in Tesla, Ørsted, and Vestas.
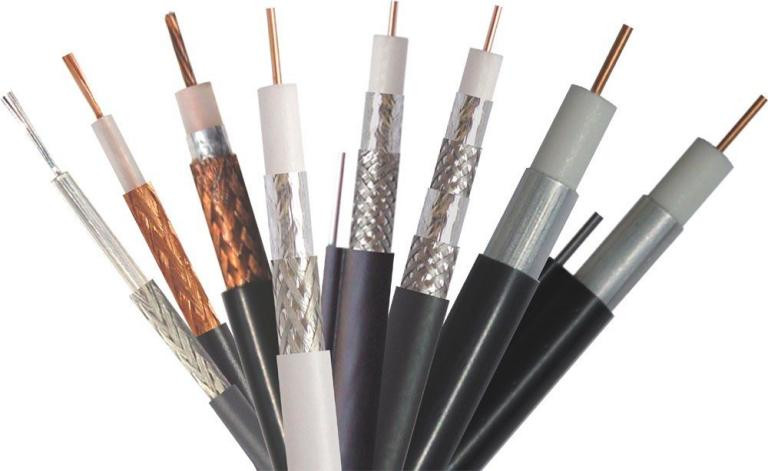
Copper Clad Aluminum Wire Manufacturers Jesper Berggreen has 237 posts and counting. See all posts by Jesper Berggreen