CUI Inc. now offers dc fans built with their innovative omniCOOL™ bearing system that offers longer life and better performance than other fan bearing options. These fans keep electronics cool in consumer appliances, large industrial machinery, and everything in between.
CUI’s omniCOOL bearing system technology addresses the limitations of ball and sleeve bearings. Its magnetic bearing structure delivers quiet operation in any orientation. The omniCOOL system’s bearing itself is hardened to resist any abrasion that does occur, and the bearing lining is heat resistant to 90° C — for far longer operating life than traditional sleeve bearings. W2e143 Aa09 01
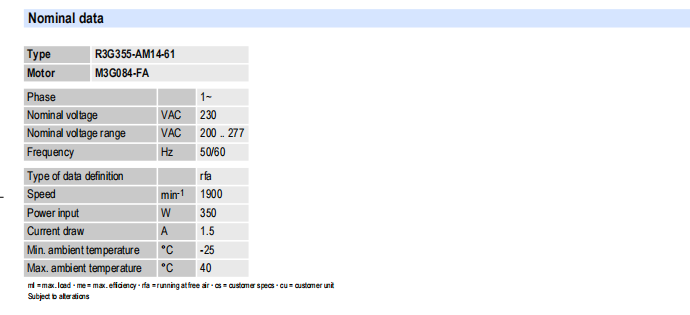
In many dc fans, a sleeve bearing carries the motor shaft — and keeps the rotor centered in the stator for a consistent airgap between the two. Oil in this small cylindrical sleeve lets the shaft turn. On the positive side, sleeve bearings are simple, resist damage from impact loading, and are relatively inexpensive.
However, sleeve bearings must be long enough to minimize rotor tilt and wobble, which makes for more contact between the motor shaft and sleeve — and that means more friction that limits fan acceleration and running speed. This also creates inefficiency in the form of drag.
Another sleeve-bearing issue is that they bear all the rotor weight resulting in inner-diameter wear over time. The sleeve cross-section will inevitably become uneven, producing an oval shape that contributes to noise and fan wobble — shortening fan life.
In fact, such bearing wear is most problematic where fans must operate on moving designs at various orientations — as on portable equipment, for example. Here, gravity isn’t always loading the rotor in one set direction, so the bearing will wear unevenly. This can exacerbate noise and wobble issues.
What’s more, most dc fan sleeve bearings have an oil ring and Mylar washer at each bore end. These retain the sleeve lubricant but introduce yet another source of friction. Plus, these elements can ultimately trap gases from the operating assembly that then solidify into nitride particles — which in turn clog the bearing and impede fan rotation.
The other bearing option for dc fans is the ball bearing — consisting of a ring of ball rollers around the shaft. These usually come in pairs to minimize friction (for quick fan acceleration and running speeds) and prevent uneven wear and the issue of rotor wobble.
In some cases, springs load the bearings so that the fan-motor rotor rides on the inner bearing, while the spring addresses any fan-blade tilt induced by the rotor weight. Springs around the shaft means the fans can operate in multiple orientations for less wear and longer MTBF than comparable sleeve bearings.
But there are issues with ball bearings as well. Unlike sleeve bearings, impact loading can damage them. Ball bearings are also more complex, costlier, and noisier than sleeve bearings.
Now, a third option for dc fans is the omniCOOL bearing system from CUI Inc. These use magnetic rotor balancing or a “magnetic structure” paired with an engineered sleeve bearing to improve performance and allow for operation at any angle.
In short, the magnetic structure sits in front of the rotor — and because its flux is parallel to the rotor shaft’s axis, it uniformly attracts the whole rotor. A support cap at the bearing bore’s front holds the shaft tip in place to serve as the point around which the rotor turns.
Using magnetic repulsion means the fan shaft and bearing sleeve don’t bear the weight of the rotor. What’s more, the magnetic field lowers the fan’s center of gravity by pulling the shaft downward to minimize tilt and wobble associated with traditional sleeve bearings, while dramatically reducing friction. The omniCOOL system’s magnetic structure minimizes shaft-and-bearing contact, which means far less need for lubricant.
The design also omits oil rings and Mylar washers and all their associated friction, noise, and consumption of space at the shaft ends. This allows gas from the rotational friction to escape (instead of solidifying and clogging the bearing). Fewer parts in the omniCOOL system means it’s easier to manufacture and quality control.
CUI Inc. fans with the omniCOOL system use a magnetic bearing to suspend the fan-motor rotor.
Addressing many of the challenges associated with sleeve and ball bearing designs, CUI’s fans built with the omniCOOL system give design engineers an alternative electronic-cooling solution. For more information, visit cui.com/omnicool-system.
Lisa Eitel has worked in the motion industry since 2001. Her areas of focus include motors, drives, motion control, power transmission, linear motion, and sensing and feedback technologies. She has a B.S. in Mechanical Engineering and is an inductee of Tau Beta Pi engineering honor society; a member of the Society of Women Engineers; and a judge for the FIRST Robotics Buckeye Regionals. Besides her motioncontroltips.com contributions, she also leads the production of the quarterly motion issues of Design World.
Browse the most current issue of Design World and back issues in an easy to use high quality format. Clip, share and download with the leading design engineering magazine today.
Top global problem solving EE forum covering Microcontrollers, DSP, Networking, Analog and Digital Design, RF, Power Electronics, PCB Routing and much more
The Engineering Exchange is a global educational networking community for engineers. Connect, share, and learn today »
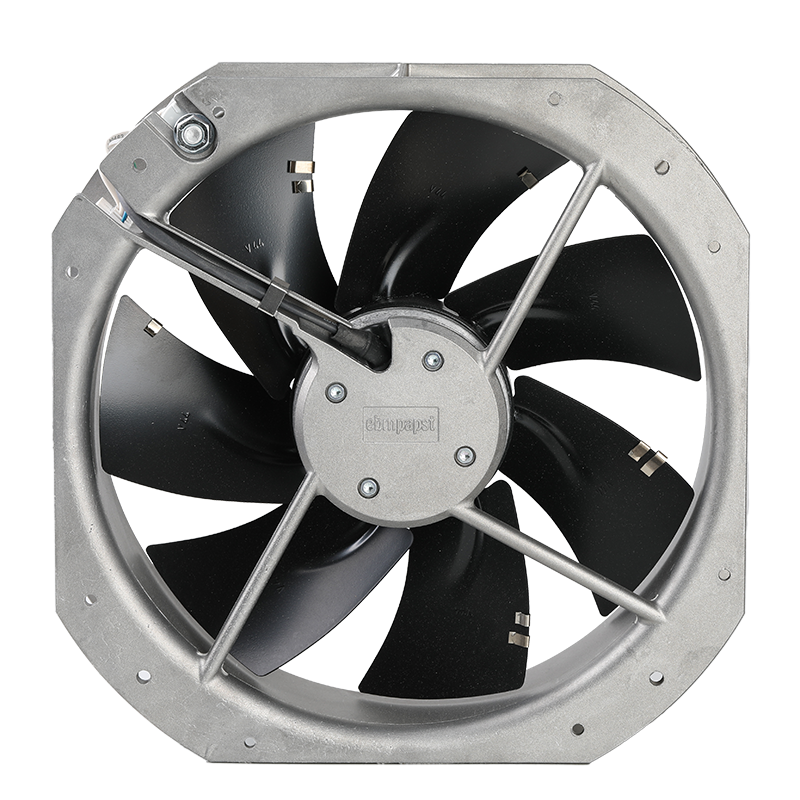
Industrial Ventilation Fan Copyright © 2023 WTWH Media LLC. All Rights Reserved. The material on this site may not be reproduced, distributed, transmitted, cached or otherwise used, except with the prior written permission of WTWH Media Privacy Policy | Advertising | About Us