Smithfield Foods announced in late July that it had constructed a new wastewater treatment system at its pork processing facility in Sioux Falls, South Dakota. According to the company, the $45 million project, which replaced much of the existing wastewater treatment system at the complex, adds additional treatment processes and capabilities and will significantly reduce Smithfield’s overall nitrogen load to the nearby Big Sioux River.
"This new state-of-the-art wastewater project reinforces Smithfield's proactive approach to implementing sustainable systems that improve environmental quality and benefit the community," Stewart Leeth, chief sustainability officer for Smithfield, said in a news release. "The investment we have made in Sioux Falls will significantly reduce nutrient discharges and improve water quality in the Big Sioux River basin." Chemical Mechanical Pulp Production Line
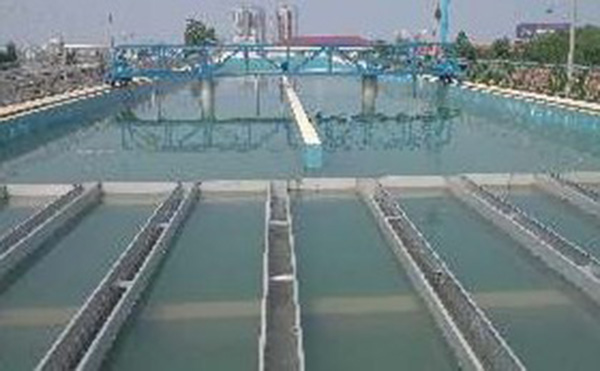
Water Technology recently had an opportunity to connect with Jason Lindquist, Smithfield’s director of environmental affairs at the Sioux Falls facility, to find out more about the new system.
Q: What led to the construction of this new wastewater treatment system at the Sioux Falls facility?
A new wastewater discharge permit was issued on July 1, 2020, requiring the reduction of nitrates in our final effluent to less than 50 mg/l. In order to complete this, the facility needed to add denitrification processes to the existing 35-plus-year-old aeration systems. After evaluating the existing equipment, the decision was made to build new aeration/anoxic basins, utilize ultrafiltration for final effluent clarification, and UV disinfection.
Q: How does the new wastewater treatment system enhance the treatment processes and capabilities at the site?
The new wastewater treatment systems are significantly more robust than the system that was installed in the early 1980s and updated over the past 40 years. When we designed the system, we designed it with the future in mind. If the need arises, we can treat about 40% more flow than we are currently treating. This gives the production facility room for growth and significantly reduces the nutrient discharge to the Big Sioux River. The previous system was capable of treating the wastewater that was coming into the plant, but with the new system we are seeing our final discharge reduced even further from historical performance with our nitrates reduced to less than 50 mg/l, the BOD reduced by 74%, and the TSS reduced by 85%.
Q: What are some of the new technologies and equipment being utilized in the new system?
We are using ultrafiltration to clean up the water going to the river. This system provides a physical barrier to ensure that our total suspended solids sent to the river are near zero. We are currently sending water to the river with a turbidity of less than 1, which in many cases is below the drinking water standard. In addition to the ultrafiltration system, we are utilizing ultraviolet disinfection. This has eliminated the need to utilize sodium hypochlorite (commonly referred to as bleach) to disinfect our final discharge. This results in a significant reduction in chemicals needed to ensure our discharge to the river is less than our discharge limitations.
We are using screw presses for dewatering solids that are generated in the wastewater treatment process. This allows us to increase the solids content of the final product which is transported to farmers’ fields as a fertilizer. This reduces transportation resources as we are hauling the same dry tons but the reduction in water reduces the total tons being hauled to the field.
Q: Permit limits related to nitrates and ammonia are becoming more stringent. How does the new wastewater system specifically address these types of regulatory requirements?
The permit issued in 2020 implemented a nitrate limitation that required us to reduce our nitrate discharge to 50 mg/l on average. This required a reduction of approximately 70-plus%. In addition to limiting the nitrates, the ammonia limit was also reduced by up to 30%. The new Biologic Nutrient Removal system is designed to have both an aerobic and an anoxic zone. The previous system had an aerobic system which very effectively removed ammonia and converted it to nitrates. In the new system, we added an anoxic zone and increased the circulation rate from 100% to 400%. That means that the system recirculates every gallon of water approximately four times before it is discharged to the Big Sioux River. This ensures that we get 70-plus% reduction of the nitrates. The byproduct of the system is nitrogen gas that is released into the atmosphere, which is already 78% nitrogen. Since the permit came into effect on July 1, 2023, we have shown a 60% reduction in our ammonia discharge on a system that was already operating 88% below our permit limits. The system is consistently running at 40 mg/l nitrates, well below our permit limit of 88 mg/l on a daily basis and 50 mg/l on a monthly average.
Q: Can you explain the denitrification process and why that is such an important aspect of this system?
We use the same bugs to treat the wastewater in the denitrification process as we do in the nitrification process. The difference is that we alter the amount of oxygen that is available for the bugs. In an oxygen-rich environment, the bugs will turn the ammonia in the wastewater into nitrates. When the oxygen is changed so there is little or no free oxygen, they eat the nitrates, harvesting the O2 off the nitrate ion while they chew up the organic material. To have the system reduce nitrates to the needed levels for our permit, we recirculate every gallon of water approximately four times through the process. We need both the aerobic and anoxic portions of the system to change all the ammonia into nitrates and then get 70-plus% reduction of the nitrates into nitrogen gas.
Q: How does the new system compare to the previous system in terms of both capacity and nutrient reductions?
The previous system was well designed to treat the wastewater to the standards of the previous permit. Over the course of 35-plus years, it had been upgraded to meet the permit limitations that had progressively gotten more stringent. At the time of the switch-over, we typically operated at 88% below our ammonia limit and 71% below our BOD limit. With the new permit, we had to bring our nitrates down to a monthly average of 50 mg/l. This is a 70-plus% removal of nitrates. This change to the system allowed us to achieve this nitrate reduction and has demonstrated more effective removal of organic loading (BOD discharges reduced by 74%) and ammonia (ammonia discharge has reduced 60%) than the previous system. Additionally, we added the ultrafiltration system which reduced our TSS by 85% from the previous system.
Q: How does this project align with the company’s approach to sustainability and environmental stewardship?
Smithfield is committed to 100% compliance 100% of the time. But this project goes beyond compliance. With the startup of the new system, our ammonia discharge is routinely running at 5% of our permit limit and 60% less than our old system discharge. Our BOD shows a similar story, routinely operating at 8% of our limit and 74% less BOD than the previous system. The TSS has been reduced even further with operations at 5% of the permit limit and an 85% reduction from the previous system. At Smithfield, we say that Good is What We Do, and this project embodies that.
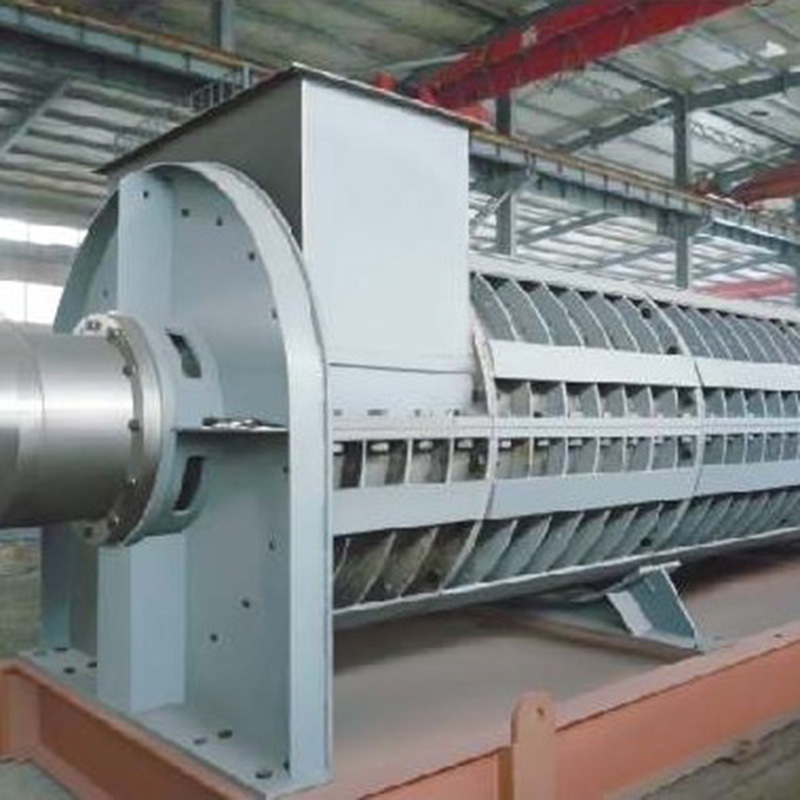
Drum Filter Jason Lindquist is Director – Environmental Affairs for Smithfield Foods supporting environmental and sustainability activities at seven facilities across the upper Midwest including the Smithfield Sioux Falls plant. He has been in this role since June 2019.