Plastic Ingenuity started in a garage in 1972 and through a commitment to developing best-in-class products stands today as one of the largest custom thermoformers in the world. #processors-edge
What was started by Joe Kuehn with a $5,000 loan from family members and a rented garage in Madison, Wisconsin, in 1972 is today one of the largest custom thermoformers in the world and, by some accounts, the largest in North America. And, by many indicators, it’s aptly named. Tail Light Housing
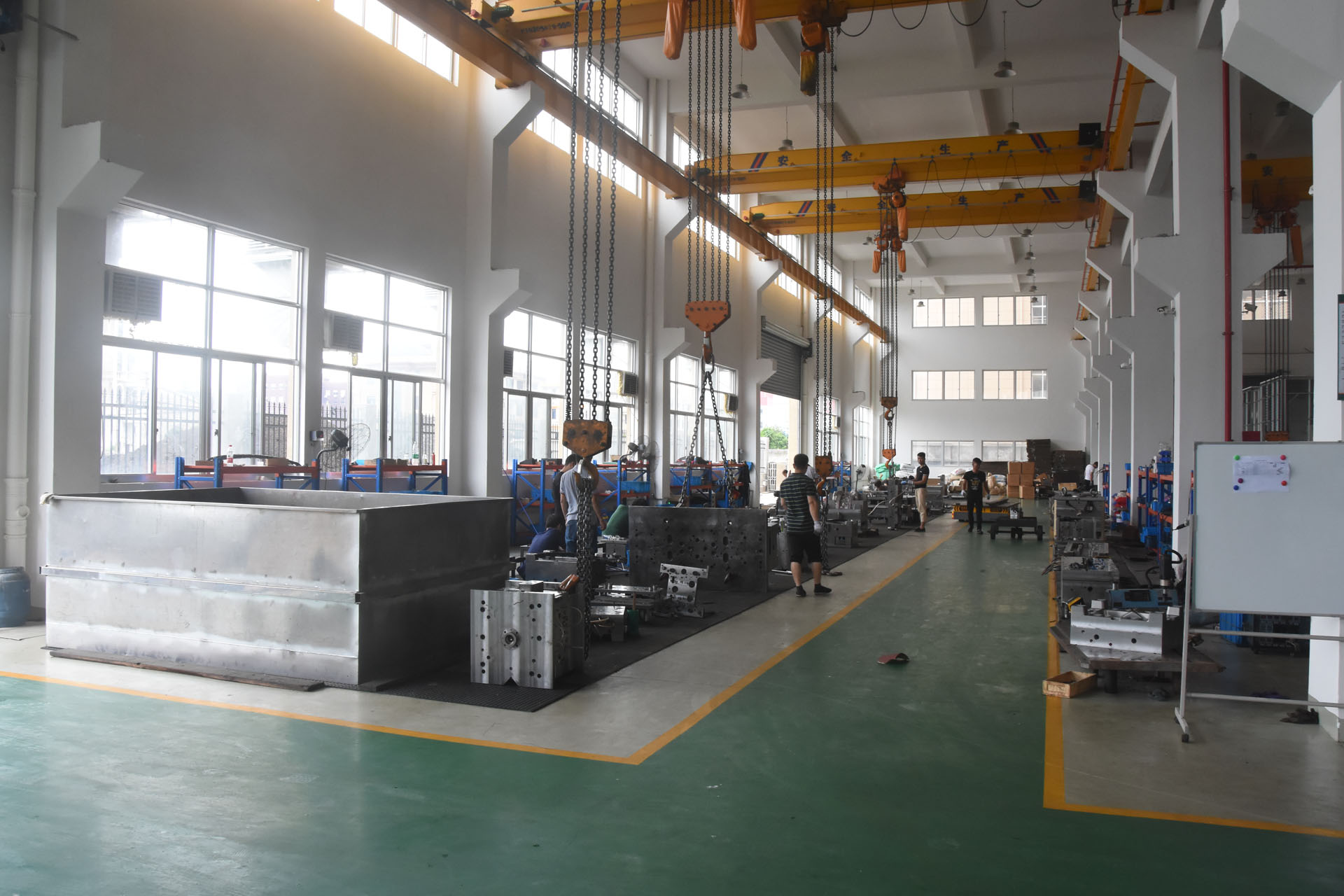
Plastic Ingenuity has built a business that from day one has been led by engineers with an unwavering commitment to innovative, highly customized, sustainable packaging solutions for customers in the food, health care and consumer goods industries.
Kuehn started with one small machine that he built; he built his own tooling, too. A year in, recalls Zach Muscato, the firm’s corporate sustainability manager, Kuehn had second thoughts about his venture and was about to close shop. Then, he landed a big project with a cheese manufacturer for a thermoformed package. And, as Muscato puts it, “that just reinvigorated everything and led to this rapid phase of expansion.”
From concept to final product, Plastic Ingenuity does everything in-house — from collaborative product design, to prototyping, to production — all in a compressed cycle. Says Glenn Petrie, the company’s commercial director– Healthcare, “We have engineers on staff with doctorate degrees to help develop or work on new and unique solutions to meet the customers’ needs. We can turn a prototype around in less than a week, in a variety of materials. I feel we have the capabilities to serve our customers in a much more holistic manner than most of our competitors.”
Today, the company has seven production facilities throughout North America (five in the U.S.) and is headquartered in Cross Plains, Wisconsin. Muscato calls these plants “satellite facilities” that were all strategically located in proximity to a customer base. Plastic Ingenuity runs 67 thermoformers companywide, all of which it built from scratch. Says Muscato, “We'll buy a stripped-down frame and add electricals and controls to basically bring the machine to life.”
At seven plants, Plastic Ingenuity runs 67 thermoforming machines, all of which have been built in-house. Photo Credit: Plastic ingenuity
Muscato adds, “We also build our own tooling. While other thermoformers build their own tooling, we build everything: the die-match metal dies, the steel-rule dies, the forming components. That allows us to control every aspect of the process.” Plastic Ingenuity is also vertically integrated on the front end, as it extrudes most of its own sheet stock, focusing on PET, PP, PS and other materials. The thermoformer is also investigating biopolymers, not just PLA and PHA but also PET and PP made from biomass.
Joe Kuehn died in a plane crash in 1995, and his brother Tom, who had been with him from the start, took over the reins until recently retiring as CEO. That title is now held by Tom’s son, Dan. Remarkably, in the company’s 50-plus-year history, it has never had a single layoff.
Earlier this year, Plastic Ingenuity received ISCC Plus certification, Muscato notes. ISCC PLUS relates to the circular economy for plastics, enabling the use of feedstocks derived from recycled plastics. More recently, it had passed its final audit and received ISO 14001 certification covering its environmental management system.
Muscato continues, “We have also gone through a very extensive process this year for accounting for our greenhouse gas emissions, so we can tell customers ‘Here's the inherent carbon that’s in the product that we provide you.’ More customers need that because their customers are asking for it.”
Thermoformed packaging for food is among Plastic Ingenuity’s core markets, the others being health care and consumer goods.
Plastic Ingenuity is also actively involved in advanced recycling initiatives. As Muscato notes, the company is a member of the Healthcare Plastics Recycling Council (HPRC).
“We have this multiyear pilot project where we’re collecting plastic waste from health-care facilities in the form of flexible films, rigid packaging, a variety of mixed-stream plastic waste,” Muscato explains. “Then, we send this stream to various advanced recyclers. And we're finding things that are troublesome for mechanical recyclers, like paper labels, that while they do hinder the advanced recycling process to a certain degree, there's much more flexibility to what can be processed in those types of technologies versus just mechanical recycling. We see a lot of potential uses for those emerging techniques.”
Plastic Ingenuity has also developed a process for working with customers for their specific sustainability objectives. Muscato elaborates, “We will meet with our customers or prospective customers, get a better understanding of what their goals are when it comes to sustainability and packaging. And from that we’ll create a road map for them for specific applications to say, all right, here are the goals that you have in place. Here’s where you’re at today with your current packaging. Here are these various solutions that we can collaborate with you on.”
He adds, “Maybe the solution is using more PCR, maybe it's down gauging, maybe it's looking at recyclability and how to improve recycling in practice. Whatever it may be, we can then pull out our tool kit to really create that road map for them to take them to where they need to be per their corporate level goals. But, sometimes we'll be working with customers that maybe don’t have goals, but they realize they need to do something. So, in those cases we’ll first direct them to their customer’s goals, the big retailers, to help them get a sense of what they need. Then, we can create a road map around that.”
Compact, flexible and configurable robotic system is said to be the first to enable thermoformers to fully automate product handling after a non-servo trim press.
Uniquely secure latching expands applications for Jamestown Plastics’ patented clamshell package design.
Productive Plastics has created an extensive collection of 3D printed manufacturing aids that sharply reduce lead times.
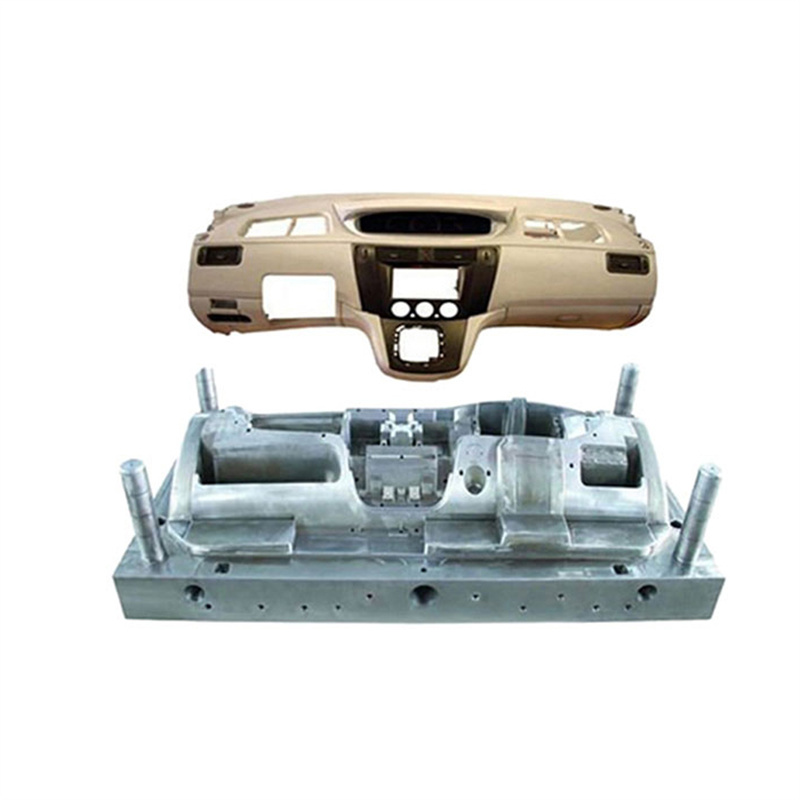
Car Headlight © 2023 Gardner Business Media, Inc. Privacy Policy [Log On]