We use cookies to enhance your experience. By continuing to browse this site you agree to our use of cookies. More info.
When it comes to storage tanks, the size presents a unique challenge. Usually, smaller storage tanks are prebuilt and shipped to the site. Agitator Mixer Tank
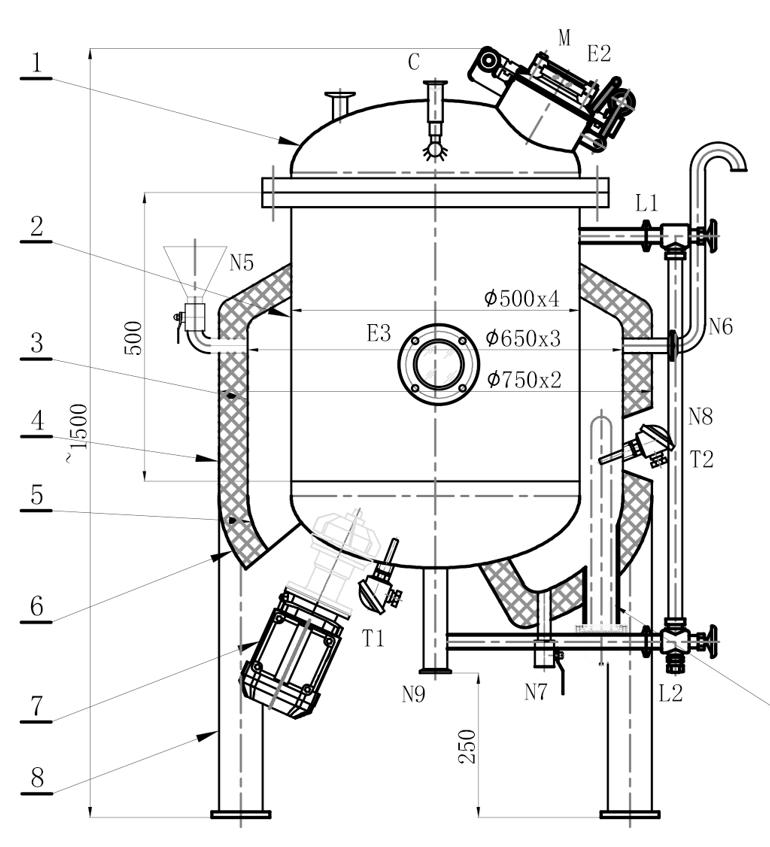
However, a different approach is required for larger tanks, which have a capacity of hundreds of thousands of gallons or more. Due to width and height restrictions limiting road transport, these tanks are assembled on-site using prebuilt sections known as Field-Erected Tanks.
The field-erected tanks are prominently utilized in the oil and gas industry. A typical refinery image includes a tank farm consisting of numerous large tanks that store different hydrocarbons, each with a capacity of millions of gallons.
Nevertheless, other industries also employ these structures. Chemical plants, for instance, have field-erected tanks on their premises to contain the necessary quantities of components and finished products required to meet industrial-scale demands.
Although less common, the food and beverage industry relies on multi-story, high-volume storage tanks. Large fermentation tanks adorn the exteriors of significant breweries, while prominent food processors employ them to store substantial amounts of ingredients such as vegetable oil and water.
Image credit: Shutterstock / Mehmet Cetin
The size of a field-erected tank depends on its purpose and location. This flexibility offers a significant advantage, allowing customization according to specific needs. Unlike infrastructure concerns related to transportation limitations, the tank's dimensions are not restricted.
Instead, the size is determined by the amount of land allocated for the tank and the number of fabricated sections that must be transported for construction. The tank owner can source the most cost-effective prefabrication options from various locations by selecting a well-situated location.
Compared to their in-ground counterparts, field-erected tanks provide long-term benefits. Being above ground, they are easier to maintain and inspect. Timely identification and resolution of corrosion or other storage issues can help prevent significant environmental spills and contamination.
Consequently, several states are now prohibiting the construction of new in-ground tanks and even mandating their replacement with above-ground storage facilities.
The prevention of tank failures starts during the construction phase. Although these large tanks can be made from plastic or composite materials, the majority are constructed using carbon steel or stainless steel.
The choice of material depends on what will be stored. However, it is essential to properly treat the tank's surface, especially the welds, before commissioning. This treatment maximizes the tank's service life and prevents the weld sites from becoming sources of corrosion or failure.
Since each tank is unique in terms of structure, size, and purpose, there is no one-size-fits-all approach to surface treatment. Tanks that contain corrosive substances require different treatment than those storing neutral contents. The tank's physical size also determines the preparation method.
Treating the entire surface area may be cost-prohibitive due to its sheer magnitude. In such cases, only the welds undergo pickling and passivation to remove the heavy oxide film formed during welding.
In certain situations, this process involves applying a chemical and passing an electric current through the electrolyte and metal for electrolytic cleaning, which eliminates free iron and weld color.
Sometimes it is more cost-effective to apply pickling gel to each weld and the surrounding heat-affected area. In some instances, specific welds on one section of the tank are treated while other sections are welded to the structure.
In other cases, cleaning the entire surface is necessary, especially for tanks intended to store liquid oxygen. Thorough cleaning is crucial to eliminate any potential contamination, as even a technician entering the tank can introduce foreign debris.
Given the range of situations and conditions, involving the experts from Astro Pak during the planning stages is beneficial.
Their extensive institutional knowledge developed over the past six decades greatly reduces the likelihood of unforeseen issues and helps plan a treatment program that ensures the tank is ready for commissioning as scheduled.
Similar to smaller steel and stainless steel systems, field-erected tanks operating under specific conditions benefit from regular passivation and cleaning as part of their ongoing maintenance.
While a tank used for storing crude oil may not require cleaning, a tank utilized for fermentation or ingredient storage necessitates a scheduled servicing routine. Compliance with the standards set by the Food Safety Modernization Act of 2011 is mandatory for all food and beverage companies.
Modern tanks designed to store ingredients or final products are typically equipped with an integrated Clean-in-Place (CIP) system, which facilitates the removal of any remaining contents between batches. However, even with such systems in place, it is advisable to implement more comprehensive treatments.
The presence of rouge, often characterized by an orange-red color, indicates a failure or loss of corrosion resistance in a steel component somewhere within the system. Identifying the source of the issue is crucial, and prompt action must be taken to address the problem.
If the rouge has spread throughout the system, a higher level of cleaning is required, surpassing the capabilities of self-performed cleaning methods. Neglecting to tackle this problem can lead to system failure or product contamination, both of which can be costly outcomes.
As mentioned previously, stainless steel is not impervious to rust. However, it exhibits high rust resistance due to its passive layer. This natural barrier can be further strengthened through the process of passivation. By reducing the likelihood of rouge formation, the overall lifespan of the system's physical structure can be prolonged.
If any modifications are made to the tank over its service life, it is crucial to treat the affected areas through pickling, electrolytic cleaning, and passivation. This preventive measure ensures that these areas do not become weak spots or potential sources of failure.
Taking a proactive approach to tank maintenance is an instance where investing in protection outweighs the potential costs of remedial measures.
Due to their ability to be customized for specific operations, locations and purposes, as well as their relatively straightforward construction process, field-erected tanks are likely to continue being a common solution for bulk liquid storage in various industrial-scale applications.
Given their significant investment and critical role in a facility's operational plans, it is essential to take steps during both the construction phase and the tank's operational lifespan to maximize its availability and longevity.
Properly preparing the tank's welds and interior surfaces can reduce the risk of failures resulting from construction defects or material weaknesses.
This not only helps prevent costly environmental issues or product loss but also safeguards the tank investment itself, ultimately maximizing its return on investment.
This information has been sourced, reviewed and adapted from materials provided by Astro Pak Corporation.
For more information on this source, please visit Astro Pak Corporation.
Please use one of the following formats to cite this article in your essay, paper or report:
Astro Pak Corporation. (2023, June 26). How to Design, Build and Maintain Field-Erected Tanks. AZoM. Retrieved on January 01, 2024 from https://www.azom.com/article.aspx?ArticleID=22757.
Astro Pak Corporation. "How to Design, Build and Maintain Field-Erected Tanks". AZoM. 01 January 2024. <https://www.azom.com/article.aspx?ArticleID=22757>.
Astro Pak Corporation. "How to Design, Build and Maintain Field-Erected Tanks". AZoM. https://www.azom.com/article.aspx?ArticleID=22757. (accessed January 01, 2024).
Astro Pak Corporation. 2023. How to Design, Build and Maintain Field-Erected Tanks. AZoM, viewed 01 January 2024, https://www.azom.com/article.aspx?ArticleID=22757.
Do you have a question you'd like to ask regarding this article?
AZoM.com - An AZoNetwork Site
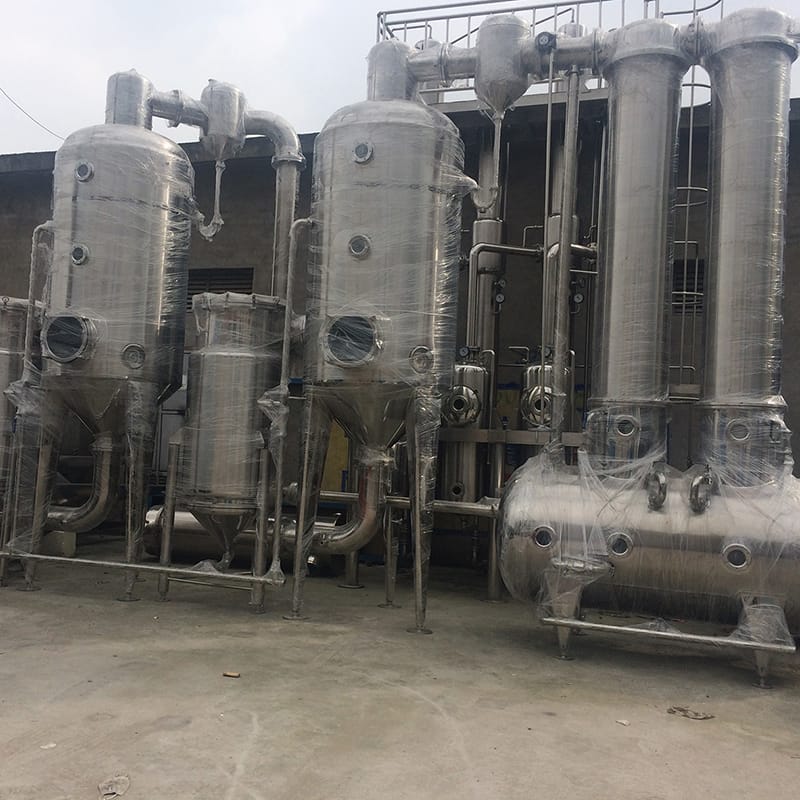
Falling Film Evaporator Ethanol Owned and operated by AZoNetwork, © 2000-2024